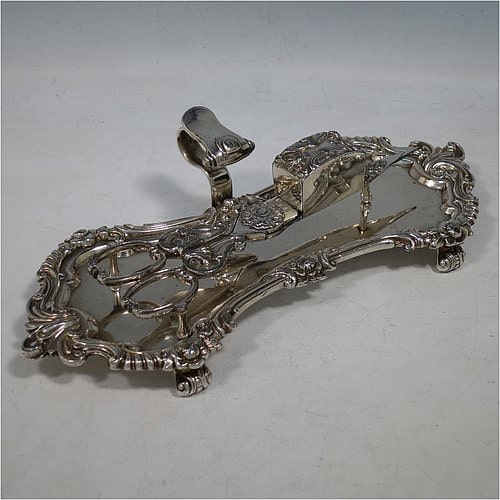
The object was first smoothed and thoroughly cleaned. It was them heated in a charcoal fire and afterwards submerged into first a solution of salt-ammoniac and then into a molten tin. This completed the fusion of the steel and tin and the item was allowed to cool.
A sheet of silver which had been hammered to the thinness of foil was then used to cover the item. It was smoothed carefully and pressed unto place by means of a hot soldering iron, which caused the tin to melt and fuse to the silver. Overlapping edges of silver were swept away. Places where the silver met were carefully fused and burnished so that all seams were totally invisible.
There were two disadvantages to close plate.
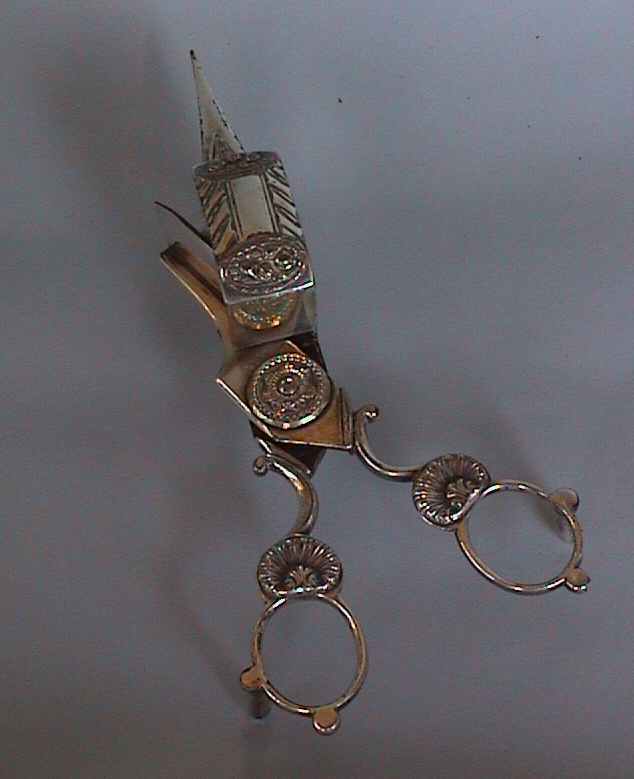
The second was that, if it came in contact with dampness, the steel or iron might rust and the plating would peel off.
Objects made in close plate were knives, small cutlery handles, spoons, forks, spurs, button, buckles, in fact any object where strength was required. Even after fusion plating was introduced, buckles continued to be manufactured by the close plating process as the steel base was harder and wore longer.
This 'close plating' scissor action candle snuffer stands on three feet and has fruits and floral ornaments with a pair of shells.
This snuffer is unmarked but very likely has English origin and was made between the end 1700's / beginning 1800's.
The snuffer is coupled with an 'old Sheffield' tray. The candle snuffer is 7 in. long (cm. 18).
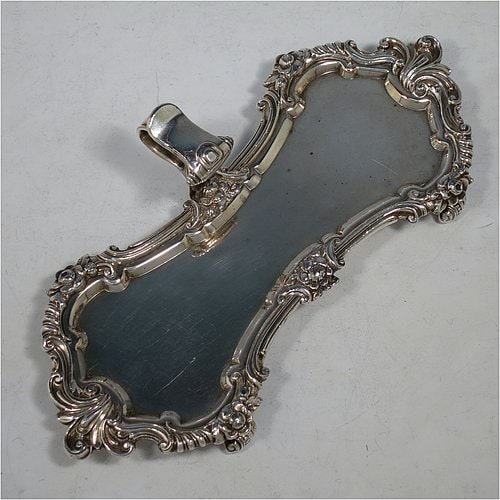